Streamlining Turnaround Maintenance with Efficient Work Order Management: A Comprehensive Guide
- Harsh Tannu
- Aug 9, 2024
- 4 min read
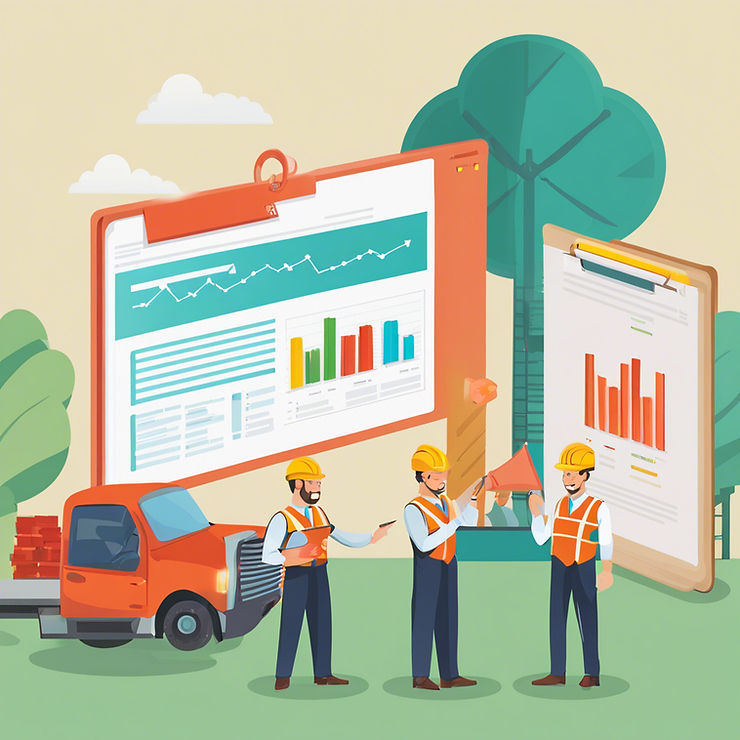
Managing turnaround maintenance work orders is often a complex and challenging process. The intricacies of handling hundreds of items, ensuring accuracy, and maintaining smooth operations can become overwhelming. As someone who has navigated these hurdles, I’ve discovered effective solutions that have transformed our work order management system, improving both efficiency and accuracy. In this blog, I’ll walk you through the challenges we faced and the innovative solutions we implemented to streamline our turnaround maintenance operations.
The Challenge of Work Order Management in the Warehouse
Handling work orders in a warehouse environment comes with its own set of challenges. Traditionally, warehouse users create work orders in the system, which may be individual or grouped based on specific needs. Although this process seems straightforward, the real complexity arises during the execution phase within the warehouse.
Planning Complexities
Planners are often required to plan hundreds of items per work order. When an item is planned, it becomes "hard committed," meaning that its quantity is reserved from inventory and cannot be utilized elsewhere. However, a common issue arises when planners do not have confirmation on the items they plan, leading to frequent amendments in the item list. These changes complicate the process and often result in warehouse users mistakenly issuing items to incorrect work orders.
The Solution: Introducing a Draft Planning Application
To address the complications of handling work orders, we developed a draft planning application. This tool is designed to allow planners to operate in a draft mode, where they can plan items without immediately committing inventory. The process becomes significantly more efficient, as it allows for flexibility and accuracy in planning.
How It Works
Draft Mode Planning: Planners can plan items without immediately committing inventory, allowing them to make necessary adjustments before finalizing the work order.
Confirmation & Commitment: Once items are confirmed, they can be moved to the actual work order planning phase, where the inventory is then committed.
This solution drastically reduces the need for amendments and ensures that inventory is allocated correctly, leading to a more streamlined and error-free process.
Streamlining the Picking Process
Once the planning phase is complete, the next challenge lies in the picking process. Initially, the process was manual, with warehouse users printing pick slips, locating items, and then manually updating the system. This approach was not only time-consuming but also prone to errors.
Traditional Picking Challenges
Manual Process: Users would print a pick slip, locate the items in the warehouse, collect them, and then update the system manually, leading to a high chance of errors.
Missed Items: Despite using the system, items often got missed during the picking process.
The Solution: Barcode Integration and Handheld Devices
To streamline the picking process, we implemented a barcode system across all locations, along with the integration of handheld mobile devices.
How It Works
Barcode Integration: Each item location now has a barcode that includes lot and item information.
Handheld Devices: Warehouse users use handheld devices to select the work order and receive precise location information for the items to be picked.
Direct Transaction Submission: After scanning the barcode and entering the required quantity, the transaction is submitted directly from the handheld device.
This system automatically prints a label, which is attached to the trolley or bag where the picked items are stored. This ensures that the correct items are moved to the designated delivery location, minimizing errors and improving efficiency.
Enhancing Communication and Quality Control
Effective communication and stringent quality control are crucial for smooth warehouse operations. To further streamline our process, we introduced an email notification system and automated quality check certificates.
Email Notification System
Real-Time Updates: Responsible personnel receive email notifications regarding picking and delivery activities, ensuring that everyone is informed and accountable.
Quality Control Enhancements
Automated Quality Check Certificates: Quality check certificates are automatically printed, ensuring that every item meets the required standards before it is issued.
These enhancements have not only improved communication but also ensured that quality control measures are consistently upheld throughout the process.
The Impact: Improved Efficiency and Accuracy
By addressing the challenges of turnaround maintenance work orders with innovative solutions, we have significantly improved the efficiency and accuracy of our work order management system. The implementation of a draft planning application, barcode integration, handheld devices, and enhanced communication tools has led to a more streamlined, reliable, and error-free maintenance process.
FAQs
What is turnaround maintenance?
Turnaround maintenance refers to the scheduled shutdown of equipment or facilities for repair, maintenance, and inspection purposes. It is a critical process in industries to ensure the safe and efficient operation of machinery.
How does draft planning help in work order management?
Draft planning allows planners to create work orders without immediately committing inventory, providing flexibility to make adjustments before finalizing the orders, which reduces errors and ensures accurate inventory allocation.
Why is barcode integration important in warehouse management?
Barcode integration simplifies the picking process by providing precise location information and automating transactions, reducing manual errors, and enhancing efficiency in warehouse operations.
How do handheld devices improve the picking process?
Handheld devices allow warehouse users to access work order information, scan barcodes, and submit transactions directly from the warehouse floor, streamlining the process and minimizing errors.
What role does communication play in work order management?
Effective communication ensures that all team members are informed and accountable, reducing the chances of errors and improving the overall efficiency of the work order management process.
Why are quality check certificates important?
Quality check certificates ensure that every item meets the required standards before being issued, maintaining the integrity and reliability of the maintenance process.
Conclusion
Managing turnaround maintenance work orders can be complex, but with the right strategies and tools, it is possible to streamline the process and enhance efficiency. By implementing draft planning applications, barcode integration, handheld devices, and improving communication, we’ve transformed our work order management system, leading to more accurate and reliable operations. These improvements not only reduce errors but also ensure that maintenance activities are carried out smoothly and effectively.
Comments